Motor Project # 16 - Timing Cover
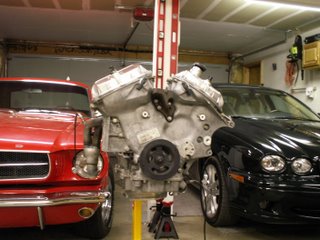
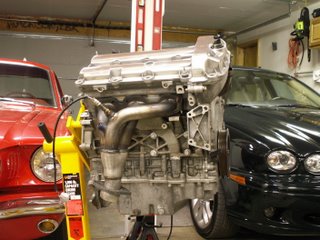
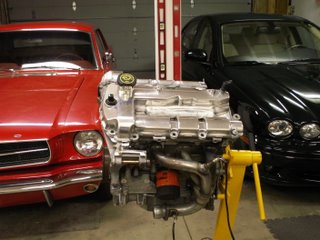
Jaguar Engine Project
Now let's time! To retime the right bank there is the easy way or the Jaguar JTIS way. I'm going to show you the easy way because if you try to read and follow JTIS, it'll make you crazy, your hair will fall out, your fingernails will grow to 12 inches long and we'll have to visit you in a special place and wipe the oatmeal off your chin...I'm sure you don't want that!
All of the JTIS assembly stuff (Engine - 303-01; steps 28 through 31) are pretty much malarchy! The clock settings are mostly meant to put the intake/exhaust cams (one bank at a time) in the most relaxed positions. The actual timing of the intake/exhaust cams to the crankshaft is never really spelled out and there is a significant chance the engine will not be timed correctly following these rote instructions. Never is the intuitive instruction given here.
Principles of Timing a Duratec: If you forget everything I've ever said, just DON'T forget this:
For the right bank: 23 chain links from the crank keyway to the exhaust cam timing mark, another 15 links to the intake timing mark.
For the left bank: 23 chain links from the crank keyway to the INTAKE cam timing mark, another 15 links to the exhaust timing mark(intake/exhaust cams reversed left/right banks). It's just that simple!
With this information you can practically put a blindfold on and time this engine with tactile skills, perfectly every time. Here are some subordinate rules:
First step, assemble the stationary chain guide. It is the one piece cast aluminum frame containing the intake VVT pump solenoid. It has three bolts, one of which gets tightened first. Also, don't forget the small dime sized o-ring between the pump and the oil passage that feeds the the VVT. Here is a picture.
The bolt that gets tightened and torqued first is the one directly under the exhaust cam sprocket. However, you still want to hand tighten all three, the other two are top/bottom of the chain guide. The reason you're torquing the bolt under the cam sprocket first is because it seats the o-ring with the VVT oil passage. JTIS torque spec is: 25 nm.
Now you're ready to place the chain on the sprockets. The relative ideal position for the right bank timing is: crankshaft keyway 7 o'clock (make that pm not am...nah, only kidding about the pm), exhaust mark at 8 o'clock pm...nah still kidding, and intake mark at 1 o'clock. This is just where we positioned everything to disassemble.
Place the chain (so it will rotate in the same direction it was removed) over the intake/exhaust sprockets. Start with the mark on the exhaust cam and count 15 links to the intake cam. This now puts the two cams in time with each other.
If you look closely at this picture, click to enlarge, you'll see the white dot mark on the exhaust cam sprocket, and the white dot mark on the intake cam sprocket is smaller, almost straight up at 12 o'clock. You can count the 15 links in the picture.
Now continue to thread the chain CLOCKWISE over the stationary chain guide and engage with the crankshaft sprocket for the right bank. Remember, you need 23 links from the keyway to the exhaust timing dot. The chain will seem very large and you'll have plenty of room to move it because the adjustable chain guide is not installed at this point.
See this picture to view the chain and timing to this point. Before the adjustable guide is assembled, the link count and the slack must be taken up all in one direction - what direction? This is a test. CLOCKWISE from the exhaust timing dot all the way around to the crank keyway. If there is too much slack on the stationary guide then turn the crank slightly CLOCKWISE (See how easy this is). If there is not enough slack to make the 23 tooth count, then rock the intake/exhaust cams together back forth until you can make this count.
Now this will sit for a moment so we can prepare the tensioner. The tensioner is a LOAD/LOCK design. It has a sprung piston that puts tension on the adjustable guide and a secondary ratchet locked stop to keep the chain from gaining slack under load. To load the tensioner, fully collapse the piston in a bench vise, then the fixed ratchet stop must be released and placed down at the shoulder of the piston. With this, a slot in the ratchet stop will appear through an inspection hole in the body of the tensioner. Place a paper clip, or drill rod in the inspection hole and this will hold the piston and ratchet in the fully collapsed position. Here is a picture of the tensioner loaded and locked. I used a small drill bit as my paper clip.
Now the tensioner along with the adjustable chain guide can be assembled. The guide just rides on a dowel pin and, without the tensioner in place, has plenty of freeplay for assembly. At this point you can push on the guide until it bears pressure on the chain and you'll see the right bank timing really coming to life now. As you hold it against the chain, now is a good time to recheck the link timing. Start at the crank keyway and count (how many links)? to the exhaust sprocket dot. Continue counting (in what direction)? and (how many links)? to the intake white dot. If everything is what you now know it should be, then you're ready to install the tensioner. Use the two bolts coated with anti-seize, thread them in by hand. There should be some play for the guide as the piston is still fully collapsed. Tighten the two bolts to (JTIS) 25 nm. Before you release the drill bit (to release the piston), there is a recess in the guide where the piston rides. There is enough play in the guide that it is possible for the piston to sit outside this recess. Once that is in place, release the drill bit. The piston will exert the correct amount of pressure to the guide at this time. Finally move the secondary ratchet stop in place under the guide recess and Voila!...Timed!
Here is a picture of the tensioner in place, torqued, just before the drill bit is released.
One final step: Rotate the crankshaft two complete turns (what direction)? to approximately the same place 7 o'clock pm (get you with that every time don't I), and recount 23, 15, to make sure you're timed correctly.
Well, that's quite the round about way (and the JTIS way) to do a valve adjustment on the V6. All together several hours of labor (Jaguar book says 5/6 hours' labor) and, again, about $400 retail in parts which includes just two shims.
How about a shortcut. One that only involves removing the valve covers then removing replacing the shims directly under the cams without removing them. Most manufacturers make a tool for this. It holds the bucket down so the shim can be removed when the cam lobe is opposite the shim. Talking to a few technicians, there is a tool like this for the V8, some talk about a tool, maybe, for the S-Type...Long story short, no one really knows and JTIS doesn't for sure.
With the cam lobe opposite the shim, reach back behind the cam with a flat blade screw driver, taped with black electrical tape. You need to catch the very edge of the bucket (it's a delicate operation). Force the bucket down in its recess, use a strong industrial magnet to catch the shim, it can be dislodged and removed. With the shim out you can release the screwdriver and no contact with the cam is made. Select the correct shim. Once again, place the screw driver on the edge of the bucket, depress (doesn't take a lot of pressure), slip the new shim in. Make sure it's seated in the bucket, release the screw driver...Voila!
Here is a picture with the screw driver in place and the new shim ready to go in.
Why should you care about this project? I'm not expecting most to do their own valve adjustments, and I start with the belief that all shops are honest, but in case one is not, there is a WHOLE BUNCH of money to be made on a valve adjustment. If the shop wants to quote JTIS procedure on an X-Type, they will probably include 6 to 8 hours of labor, or more, and anywhere from $400 to $600 in parts. Then they can perform this shortcut and cut the labor down to one and a half or two hours. That's why you want to know this, even if you never DIY!
At this time I am proceeding to seal the engine back up. Next, I'll reinstall the lower end stuff removed in earlier posts. pan baffles, oil sump pick up, oil pan. I'm fairly convinced there isn't much I can do with the innards of the Duratec, even crossing over to the generic side. At least for the moment.
On the other hand, there is plenty to do outside, with intake and exhaust. I have been very busy pursuing two options for more efficient exhaust. One is a moderate design using other Duratec parts and a cat back layout. The other involves a full blown header set with cat back also. I will be previewing both options in mock up very soon. There is still a lot of work to do with building crossover pipes, etc., but I'm feeling very optimistic about the exhaust. Both options, BTW, still fully utilize the factory ECM outputs and factory mapping. Then Karl Wolf has a muffler mod that I'll include in the final exhaust mod.
Hope you enjoy.
Cost? About $15.00 in parts. Time? One hour for the simple solution. Two to three hours for the more complex solution. The great thing about these mods is that unless you know what you are looking at, the air intake looks totally stock and really does not change anything but allows more airflow. You may notice a very small increase in intake growl but it is only due to the increase in airflow, not the growl associated with an aftermarket air intake. These aftermarket intakes take air from under the hood. Some of the benefits of these kits are negated by the additional heated underhood air.
NOTE: This covers the X-Type, however, I've included two links that give fluid information for all models.
SPECIAL WARNING: The fluids used in the Jaguar X-Type are a new generation "extended life", "long life" or "sealed for life" fluids. Be VERY careful replacing any of these fluids with traditional natural petroleum or synthetic products. Some suppliers that want to sell lubricants are going to give you a recommendation if you ask for their "compatible" lubricant, but the question is bigger than that. Look at the Ford or Jaguar specification that I've listed for each component. You must ensure the replacement lubricant is compatible with the spec. For example: The new generation M2C192A Ford spec. for the differential lubricant is a much different product than just a standard 75W140 synthetic gear oil. I've put dozens of hours in researching brands, calling suppliers and assembling the information below. Save yourself some time/effort and take advantage of this work.
RE: Lubricants, Fluids, Sealers and Adhesives Description Specification. I’ve completed an exhaustive research matching Jaguar (Ford) specifications with commercial brand oils and lubricants. And I now know more than I ever wanted about fluids specifications! Ford (and Jaguar), like all manufacturers, creates an engineering specification for fluids, then usually manufactures their own or partners with a supplier. Jaguar has partnered with Castrol since 07/2004. Commercial lubricant suppliers then choose whether to offer products that meet manufacturer’s specifications. Unfortunately, not all popular brands choose to specify compliance with all manufacturers. That doesn’t mean they do not, but they don’t market products for specification compliance.
A good example of this is two manufacturers popular with the race circuit – Royal Purple and Redline. Redline makes synthetic gear lubricants for transmissions, transfer cases and differentials. They do not advertise manufacturer’s specification compliance in their product spec sheets, and they did not answer my written request for that information. Therefore, I don’t list their products and you’re on your own if you want to substitute their products for Jag/Ford specs. Royal Purple makes synthetic oils and lubricants as well as traditional oils. They too do not advertise, nor would they answer written requests for spec compliance. They actually recommend synthetic motor oil (10W 40) for manual transaxles and in compliance with WSD-M2C200-C, but call me skeptical. Again, you won’t find these products on my list. For all of my research I use the factory vehicle specifications by Jaguar. I've attached a Jaguar bulletin regarding fluids to the bottom of this post. Note the warnings about unauthorized fluids and impact on warranty. "Fluids are subject to audit on warranty claims." BTW – If anyone wants their own copy of the vehicle specifications by Jaguar, someone published the 2003 PDF version on the web. Find it at: http://jaguar.telko.ru/Vehicle%20Specification%20(1998-2003%20all%20models).pdf General Specifications from JTIS, details follow: Engine oil (EUROPE), SAE 5W-30W SS-M2C-913A – N/A in this doc. Engine oil (US), SAE 5W-30 ILSAC GF3, API SJ – See Below Engine assembly lubricant SQM-2C9003 AA EP90 – Used to assemble engine components like camshafts, bearings, etc. Any internal engine part that might have metal to metal contact on startup before engine oil can get to it. These are all greases that dissolve and go into solution with motor oil. Brands: Redline Assembly Lube; Torco MPZ Assembly Lube pn. MPZ-AL; Belray Assembly Lube Sta-Lube Assembly grease – NOTE: None of these could be verified as complying with SQM-2C9003 AA EP90, however, all are meant to be compatible with motor oil. Hose assembly surfactant ESE-M99B144-B Brands: Merpol (is a trade name). Metal surface cleanerWSW-M5B392-A Could not find a supplier SealantWSS-M4G323-A6 Could not find a supplier Spark plug grease'Neverseeze' ESE M12 A4A Brands: Permatex Anti-Seize Compound Engine Oil: JTIS Spec (US): Engine oil (US), SAE 5W-30 ILSAC GF3, API SJ 5W30 ONLY – As the hydraulically operated VVT is extremely sensitive to viscosity changes. 5W30 gives the best viscosity range results with VVT. Never use a higher W number than 5W in the Duratec with VVT. Wider viscosity ranges or weights over 30 can defeat the hydraulic oil pump under certain temperature conditions and cause it not to respond, even though the ECM sends the electronic signal to shift. Jag service intervals change oil and filter every 10K – My interval is every 5K. Brands: Castrol GTX 5W30 (Castrol is actually recommended by name and logo in the Jaguar factory specifications dated 07/2004); most other shelf oil brands. Some believe in synthetics. JTIS doesn’t really say yes or no. Probably OK to use, but don’t take that as my recommendation. Capacity: 2.5L and 3.0L. 7 US Qts. Rear Differential Oil: JTIS Spec: M2C192A synthetic, SAE 75W140 synthetic gear lubricant. The M2C192A Ford spec. is a synthetic gear oil with a friction modifier already added. You do NOT want to use a standard synthetic gear oil w/o a modifier or that does not meet M2C192A. It’s important that you don’t over or under do the modifier if you’re going to add your own. Jag calls this unit sealed for life and changes are not necessary. Not for me – every 30K to 60K miles. Brands: Sta-Lube Syn GO 75W 140 Synthetic states M2C192A compliance on the label; Capacity: 2.5L and 3.0L. 1.268 US Qts. (2.5 Pts.) Transfer Case Oil: JTIS Spec: M2C192A synthetic, SAE 75W140 synthetic gear lubricant. Jag spec, again, sealed for life. I will change every 30K to 60K along with the diff. same fluid spec in both. I’m using the Sta-Lube Syn Go ($38 for a two quart container). The two quart is enough for both diff and Xfer case. Brands: Sta-Lube Syn GO 75W 140 Synthetic Capacity: REFILL – 2.5L and 3.0L. 1.16 Pts. (18.6 Ozs.) Manual Transaxle Oil: JTIS Spec: WSD-M2C200-C Synthetic, SAE 75W90 Synthetic Gear Lubricant. This is the infamous “lifetime” lubricant specification. It is very new on the scene. Manufacturers are not hitting the commercial market with this product (or the automatic trans fluid) because the units don’t require changing. This has been particularly frustrating in research and I’ve spent the most time on both transaxles. For the manual, and coincidentally, Motorcraft has a WSD-M2C200-C compliant fluid, I suspect, could be purchased at any Ford dealer. I have yet to try, but will be my choice. Amsoil also refers to this spec as compliant. Castrol BOT 130M is compliant, but I cannot find it for sale in the states. Brands: Motorcraft XT-M5-QS (Is the best if you can find it); Amsoil AGR or TGR; Castrol BOT 130M Capacity: 2.5L and 3.0L.1.84 US Qts. (3.7 Pts.) Auto Transaxle Oil: JTIS Spec: WSS-M2C922-A1 automatic transmission fluid. From the Jaguar spec 7/2004 - Use of any other fluids may result in a transmission malfunction or failure. Intervals Normal Maintenance Not necessary. Filled for life. Severe Duty Maintenance Change the fluid at 48,000 km (30,000 miles) intervals. It was very difficult interpreting the factory spec. Then I discovered a factory bulletin online. It is attached at the bottom of this post and an excerpt is listed for brands. Shell is a popular brand in the US and it looks to be a Mercon V type fluid. Use the Shell pns. listed to match compatibility. Jatco makes their own recommended fluid, but I have no idea how one would purchase it. Brands: All of the following come from the service bulletin attached on the bottom of this post - Recommended fluids Esso LT 71141; Shell ATF 3403 M115; Shell M1375.4; MERCON V XT-5-QM ATF; IDEMITSU K17; Jatco 3100 PL085. Jatco is preferred if you can find it. Capacity: 2.5L and 3.0L. Approx 8.32 US Qts. Refill – (Initial fill 9.3 qts) Engine Coolant: JTIS Spec: WSS M97B44 D. This is compatible with long life marketed anti-freeze. Originally developed for GM, called Dex-cool, this fluid is pink/orange in colouor, not green. Long life specifies 5 year 150,000 mi changes. I don’t agree and change mine every 12 to 24 months max. Brands: Prestone Extended life 5/150. This is a new generation (pink/orange) coolant compatible with all coolants - green, pink, orange, or whatever. Capacity: 10.6 qts 3.0L and 2.5L – but expect that you might not get the entire system drained from the heater core and engine block. Brake Fluid: JTIS Spec: Super Dot 4 – From research, several manufacturers offer super dot 4, but hard to find in local parts stores. It can be ordered online from most suppliers. The motorcycle world seems to use it more commonly, so look for it at a local cycle shop. BTW - Synthetic brake fluids are becoming very popular and, just like motor oils, Jaguar doesn't say one way or another whether to use or avoid Synthetic brake fluid. The factory specifies purging the entire system every two years (VERY important as brake fluids, even synthetics are hydroscopic). My interval is once a year. Brands: Castrol Super dot 4; Belray Super dot 4; Penszoil super dot 4 – many others. Capacity: estimated less than 1 qt. with reservoir and manual clutch. The auto will use less. Power Steering Fluid: JTIS Spec: Mobil ATF meeting Dexron 3 Specification. I don’t purge or change power steering fluid, just watch for leaks or steering resistance. Sometimes a fluid change helps, but not always. Brands: Any good quality Dexron 3 commercial product. Capacity: 1.2 Qts. Approximately. RESEARCH Sources (online): Find a factory tech bulletin at: http://www.wwwboards.auto.ru/jaguar/5301.html Technical Service Bulletin No.JagA100-000413 December 2004 Subject/Concern : Jaguar - Recommended Castrol Lubricants and Fluids in Service Models : XJ Range 1998- Vin range : 812317 Onwards XK Range 1998- Vin range : 001246 Onwards S-TYPE 1999- Vin range : L00600 Onwards X-TYPE 2001- Vin range : C00344 Onwards
In this post I'll pursue those two valves and correct the clearances. I'll just cover what I need to get to those two shims. I'll put assembly in some future post; otherwise, this would take up a lot of space and pics.
The Jaguar Duratec head design is unique in its application for the X-Type. The 2.5L and 3.0L both use the same layout, except the valves are slightly larger in the 3.0L. This is a double overhead cam design with a mechanical valve train and not hydraulic as other Duratecs are. Jaguar designed a variable valve timing (VVT) feature and works by varying the cam positions of the intake cams only. Their positions change in relation to the position of the crankshaft and exhaust cams to optimize torque during the rpm range from idle to redline.
The system works using a hydraulic two-port pump design, fed with engine oil and pressure, and controlled by the ECM. The ECM sends a signal to the pumps to close one port, open the other to advance the intake cams to create the optimal combination of performance/fuel economy/emissions at certain places during the RPM/load range, then sends the opposite signal (close that port, open the first) to retard the intake cams.
These electric/hydraulic pumps (one for each intake cam) are VERY sensitive to oil viscosity, so it is important to use the "right" oil weight, otherwise, the VVT might not function even though the ECM sends signals to advance or retard. 5W 30 multi-grade is the best weight range for most driving conditions and tested to be the required weight by Jaguar. Note that the engine oil cap has 5W 30 printed on its top. If another weight oil is used in a Duratec the W should never be higher than 5W, so the only other option might be 0W 30.
Enough philosophy - let's get our hands dirty. If you remember from past posts, I have the Duratec torn down to expose the cams. It is down to the block and heads, but the timing cover was left in place. Here we'll remove the timing cover and timing chains so the intake cam can be removed, then we can finally reveal/remove the shim buckets. These shims on buckets control the valve clearance. They are a two piece design (bucket and shim). There is no way around using any special tool to depress the bucket and remove just the shim like so many other mechanical lifter DOHC designs, including other Jaguar engines. If someone has I'd like to hear from them.
So, first step is to remove the crankshaft pulley. There is a special Jaguar tool used to hold the pulley from turning anti-clockwise as the retaining bolt is broken loose. Remember, it is critical that the crankshaft only turn clockwise for two reasons - the timing chain tensioners can be damaged if they travel backwards and the journal bearings are specially ground to minimize wear in one direction. If the engine were to turn anti-clockwise, burrs might be created on the bearings - a true no, no.
I made my own special tool to hold the crank pulley using an old serpentine belt. Break the retaining bolt loose, then use a three legged gear puller to back the pulley off the crankshaft and key. After the pulley is removed, loosen and remove all of the bolts holding the timing cover in place. With all bolts out, the timing cover needs to be LIGHTLY tapped to break the gasket bonds. It's important to use something soft (such as a piece of wood) with a rubber mallet. Do not hit the cover with a hammer! Place the wood on a non-gasketed surface, then lightly tap the wood - Capish?
Here is a picture of the timing cover. It is a HUGE (and ugly), heavy aluminum casting. It will come with a crankshaft oil seal (that I will replace before reassembly), the cam position sensors, and the crankshaft position sensor. Integral to the casting are the entire mounting ears (brackets) for the alternator and the power steering pump. Be careful how you handle this piece with its bulk.
Some points of interest - there are three formed gaskets used to seal the timing cover. Keep in mind that oil is flowing behind this cover during engine operation. I've put the gaskets in place and they can be seen in this picture. Along with these gaskets, a silicone gasket material must be used in 6 places (2 places each gasket) as these three formed rubber gaskets cross no less than six part lines on the engine assembly - four places at the head/block lines and 2 places at the bedplate lines. I'll include two pictures at the end of this post with closeups of part lines. The fourth seal is the crankshaft seal. It can be seen in place. Part of the oil pan gasket (two oil pan bolts shown in place) and the valve cover gaskets
are sealed to the timing cover after its assembly.
On the lower righthand corner of the picture, I've included the crankshaft position gear. It sits freely on the crankshaft behind the timing cover and is held in place by the crankshaft pulley. Take a close look at this gear. It has two keyway notches and, yes, it CAN be installed incorrectly. Make sure the keyway notch that is used on the keyway is the one with the missing tooth - Capish?. You can see the black CP Sensor coming through the timing cover. It's a magnetic pickup and reads the teeth from the CP gear. The missing tooth tells the ECM the engine is at TDC.
OK, let's see what we've revealed by removing the timing cover. The cam timing chains are now visible and can be removed. For this project, I will only remove the timing chain for the right bank (left side bank in the picture) where my two "troubled" valves are located. Luckily, the RH bank is the outer timing chain so I can leave the LH bank in place for this project.
In this picture you can view the two intake cam electro-hydraulic pumps with the ECM sensor connectors in place. The tops of these can be seen as coming through the valve covers on an assembled running engine. The double timing chain design is a very simple, easy to time layout. Let's focus at only one side at a time. Going clockwise (always clockwise on this engine) a chain runs from the crankshaft over a curved chain track. This is the tensioner side and you can see the spring loaded tensioner block behind the curved tensioner frame. It is a ratcheted design. The spring loaded plunger puts pressure on the curved frame, then a secondary fixed ratchet plunger keeps the tensioner frame from moving backwards.
Timing (assembly) is simple and removing (disassembly) is even easier. Three marks need to be observed for each bank, one on the crankshaft (the crankshaft key), then a timing dot on the cams, one on the exhaust and one on the intake. These cam marks are made in manufacturing, however, even if they didn't exist, one can easily get this engine timed, like this:
JTIS instructions say: For the RH bank chain removal (first chain), put the crankshaft keyway in the 7 o'clock position. This will put the Exhaust cam marker dot in the 8 o'clock position and the Intake cam timing dot in the 1 o'clock position. If you did this and the cam timing dots were not in these places - why not? Because the gear ratio - cams to crankshaft is 2:1. So if the marks are not where they're supposed to be, rotate the crankshaft 360 degree to the 7 o'clock position again. Now the three marks should be in place. BTW, these JTIS instructions position both intake and exhaust cams at the ideal place where little or no cam lift is exerting pressure on any of the RH bank valves. This ideal position makes cam removal easy and puts the least pressure on the cam journal bearings. But, technically you could remove the timing chain in any position by creating your own timing marks. For the RH bank, from the crankshaft keyway, count 23 teeth on the timing chain in a clockwise direction and make a mark on the RH exhaust sprocket at the 23rd tooth. From that tooth and continuing clockwise count 15 teeth to the intake cam and put a mark at the 15th tooth in the intake cam. Knowing these tooth counts can get you timed again. The LH bank works the same way with the same count, except you are counting from the keyway clockwise 23 teeth to the INTAKE cam first, then 15 to the EXHAUST cam second. The important instruction is always go CLOCKWISE ... Phew!
OK - once you have the crankshaft and cams on the RH bank in these ideal clock positions, the next step is to remove the RH timing chain tensioner. Remove the two bolts holding the tensioner in place. This will relieve the tension on the RH bank chain. Now remove the curved tensioner frame. It just sits on a pivotal dowel pin and comes right off. The chain can now be removed, then three bolts to remove the fixed chain track on the back side of the timing train. This fixed chain track is one piece with the hydraulic VVT pump, so it all comes off with three bolts.
CAUTION: There is a small o-ring located at the oil feed for the pump between the assembly and the RH head. The recess to hold it is made in the tensioner assembly, not the head. This o-ring is smaller than a dime so it's hard to see. It must be renewed/replaced when reassembling.
Here is a picture of what it all lookes like with the RH bank chain and tensioners removed and the chain dropped. I've left the chain on the crank sprocket . Remember, you want the chain to be reassembled in the same direction as it was removed. Do not turn the chain around so it rotates backward from its original assembly. I took only one picture after I removed the RH intake cam, but so far the instructions cover only the chain removal.
Now back to the top of the engine. We need to remove the intake cam to expose the the two shims/buckets on the #1 and #2 cylinders. At this point of disassembly the cams are no longer timed to each other or the crankshaft. Remember, if you followed the JTIS steps, the cams are ideally placed so little load exists from valve springs and no piston is at TDC ... a safe place. Loosen EVENLY the cam bearing tower bolts. These bearing caps are on dowel pins so they're not going to readily come up/off with bolt removal. One of these caps is much larger than the other 3 because it not only controls cam rotation runout, but also controls camshaft lateral movement. All of these caps must be marked and must go back in the same place and same orientation. So, whatever your system is, ensure reassembly is the same as what you disassembled.
Here is a picture of the intake cam removed. I've also removed the shims and buckets from the two "problem" intakes. These come out very easily using a shop magnet. The shim and bucket is a two piece design with very close tolerances. In mechanicla engineering this fit is called a "wroking fit" with less than .0005" clearance. I needed to heat the assembly up to 200 deg F so that the oil film underneath the shim would become viscous enough to loosen the shim. Then I needed a special pair of sof pliers and magnet to assist. I tried an air blast, but that did nothing. I'll mic (micrometer) these two shims, then purchase the next smaller shim bucket size from Jaguar. In the picture, you'll notice a lot of grease. This is engine assembly grease. I've coated every moving part of the engine as a "preliminary" lube. Assembly grease greatly assists in bearing lubrication on eventual startup. It is designed to dissolve in engine oil.
Finally, here is a group picture that shows all of the parts removed to get to the buckets. From the left: the RH chain tensioner; the curved chain track; the two intake bucket shims; the fixed chain guide with the VVT pump; the intake cam from the RH bank. The chain was left on the crank sprocket as it can so easily be reversed.
Here are two closeup pictures of part lines that the timing cover gaskets must cross. The factory uses a small dot of silicone gasket material at these pointe to ensure seal. The factory gasket is not enough to prevent an oil leak. The first pic shows the inner part lines from both heads as they mate to the engine block. The second picture shows the outer RH head to block partline. This one is perticularly difficult to clean of old silicone because of a dowel pin locater used on the timing cover. The aluminum surfaces must be cleaned and prepped for the new gaskets using a soft tool as anything hard will marr the surfaces.
Now I get to go to my local Jaguar parts department and spend LOTS of money. More to come. In a future post, I'll reassemble this so that you can have a complete process for valve shim clearance correction.
If there are any questions, comments or additional discussion wanted, please email.
Enjoy!