Motor Project # 14 - Waiting to Exhale, the 1st Sequel
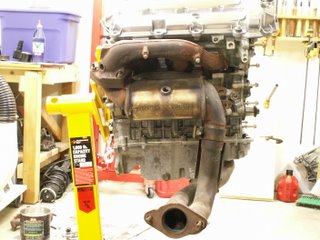
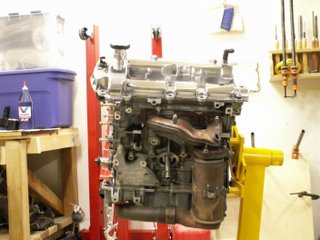
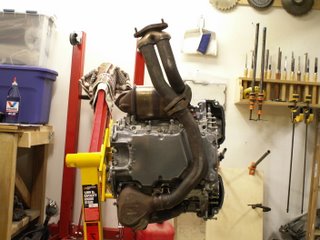

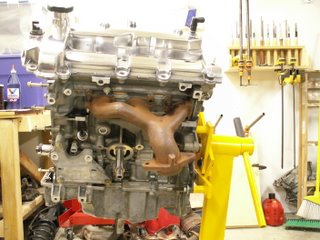
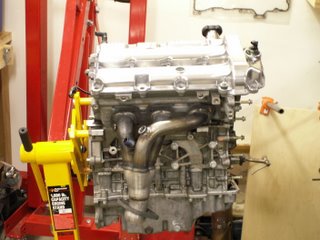
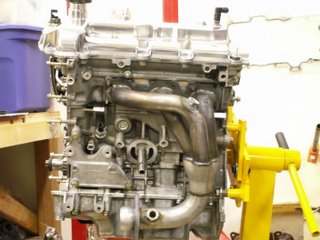


Jaguar Engine Project
Now let's time! To retime the right bank there is the easy way or the Jaguar JTIS way. I'm going to show you the easy way because if you try to read and follow JTIS, it'll make you crazy, your hair will fall out, your fingernails will grow to 12 inches long and we'll have to visit you in a special place and wipe the oatmeal off your chin...I'm sure you don't want that!
All of the JTIS assembly stuff (Engine - 303-01; steps 28 through 31) are pretty much malarchy! The clock settings are mostly meant to put the intake/exhaust cams (one bank at a time) in the most relaxed positions. The actual timing of the intake/exhaust cams to the crankshaft is never really spelled out and there is a significant chance the engine will not be timed correctly following these rote instructions. Never is the intuitive instruction given here.
Principles of Timing a Duratec: If you forget everything I've ever said, just DON'T forget this:
For the right bank: 23 chain links from the crank keyway to the exhaust cam timing mark, another 15 links to the intake timing mark.
For the left bank: 23 chain links from the crank keyway to the INTAKE cam timing mark, another 15 links to the exhaust timing mark(intake/exhaust cams reversed left/right banks). It's just that simple!
With this information you can practically put a blindfold on and time this engine with tactile skills, perfectly every time. Here are some subordinate rules:
First step, assemble the stationary chain guide. It is the one piece cast aluminum frame containing the intake VVT pump solenoid. It has three bolts, one of which gets tightened first. Also, don't forget the small dime sized o-ring between the pump and the oil passage that feeds the the VVT. Here is a picture.
The bolt that gets tightened and torqued first is the one directly under the exhaust cam sprocket. However, you still want to hand tighten all three, the other two are top/bottom of the chain guide. The reason you're torquing the bolt under the cam sprocket first is because it seats the o-ring with the VVT oil passage. JTIS torque spec is: 25 nm.
Now you're ready to place the chain on the sprockets. The relative ideal position for the right bank timing is: crankshaft keyway 7 o'clock (make that pm not am...nah, only kidding about the pm), exhaust mark at 8 o'clock pm...nah still kidding, and intake mark at 1 o'clock. This is just where we positioned everything to disassemble.
Place the chain (so it will rotate in the same direction it was removed) over the intake/exhaust sprockets. Start with the mark on the exhaust cam and count 15 links to the intake cam. This now puts the two cams in time with each other.
If you look closely at this picture, click to enlarge, you'll see the white dot mark on the exhaust cam sprocket, and the white dot mark on the intake cam sprocket is smaller, almost straight up at 12 o'clock. You can count the 15 links in the picture.
Now continue to thread the chain CLOCKWISE over the stationary chain guide and engage with the crankshaft sprocket for the right bank. Remember, you need 23 links from the keyway to the exhaust timing dot. The chain will seem very large and you'll have plenty of room to move it because the adjustable chain guide is not installed at this point.
See this picture to view the chain and timing to this point. Before the adjustable guide is assembled, the link count and the slack must be taken up all in one direction - what direction? This is a test. CLOCKWISE from the exhaust timing dot all the way around to the crank keyway. If there is too much slack on the stationary guide then turn the crank slightly CLOCKWISE (See how easy this is). If there is not enough slack to make the 23 tooth count, then rock the intake/exhaust cams together back forth until you can make this count.
Now this will sit for a moment so we can prepare the tensioner. The tensioner is a LOAD/LOCK design. It has a sprung piston that puts tension on the adjustable guide and a secondary ratchet locked stop to keep the chain from gaining slack under load. To load the tensioner, fully collapse the piston in a bench vise, then the fixed ratchet stop must be released and placed down at the shoulder of the piston. With this, a slot in the ratchet stop will appear through an inspection hole in the body of the tensioner. Place a paper clip, or drill rod in the inspection hole and this will hold the piston and ratchet in the fully collapsed position. Here is a picture of the tensioner loaded and locked. I used a small drill bit as my paper clip.
Now the tensioner along with the adjustable chain guide can be assembled. The guide just rides on a dowel pin and, without the tensioner in place, has plenty of freeplay for assembly. At this point you can push on the guide until it bears pressure on the chain and you'll see the right bank timing really coming to life now. As you hold it against the chain, now is a good time to recheck the link timing. Start at the crank keyway and count (how many links)? to the exhaust sprocket dot. Continue counting (in what direction)? and (how many links)? to the intake white dot. If everything is what you now know it should be, then you're ready to install the tensioner. Use the two bolts coated with anti-seize, thread them in by hand. There should be some play for the guide as the piston is still fully collapsed. Tighten the two bolts to (JTIS) 25 nm. Before you release the drill bit (to release the piston), there is a recess in the guide where the piston rides. There is enough play in the guide that it is possible for the piston to sit outside this recess. Once that is in place, release the drill bit. The piston will exert the correct amount of pressure to the guide at this time. Finally move the secondary ratchet stop in place under the guide recess and Voila!...Timed!
Here is a picture of the tensioner in place, torqued, just before the drill bit is released.
One final step: Rotate the crankshaft two complete turns (what direction)? to approximately the same place 7 o'clock pm (get you with that every time don't I), and recount 23, 15, to make sure you're timed correctly.
Well, that's quite the round about way (and the JTIS way) to do a valve adjustment on the V6. All together several hours of labor (Jaguar book says 5/6 hours' labor) and, again, about $400 retail in parts which includes just two shims.
How about a shortcut. One that only involves removing the valve covers then removing replacing the shims directly under the cams without removing them. Most manufacturers make a tool for this. It holds the bucket down so the shim can be removed when the cam lobe is opposite the shim. Talking to a few technicians, there is a tool like this for the V8, some talk about a tool, maybe, for the S-Type...Long story short, no one really knows and JTIS doesn't for sure.
With the cam lobe opposite the shim, reach back behind the cam with a flat blade screw driver, taped with black electrical tape. You need to catch the very edge of the bucket (it's a delicate operation). Force the bucket down in its recess, use a strong industrial magnet to catch the shim, it can be dislodged and removed. With the shim out you can release the screwdriver and no contact with the cam is made. Select the correct shim. Once again, place the screw driver on the edge of the bucket, depress (doesn't take a lot of pressure), slip the new shim in. Make sure it's seated in the bucket, release the screw driver...Voila!
Here is a picture with the screw driver in place and the new shim ready to go in.
Why should you care about this project? I'm not expecting most to do their own valve adjustments, and I start with the belief that all shops are honest, but in case one is not, there is a WHOLE BUNCH of money to be made on a valve adjustment. If the shop wants to quote JTIS procedure on an X-Type, they will probably include 6 to 8 hours of labor, or more, and anywhere from $400 to $600 in parts. Then they can perform this shortcut and cut the labor down to one and a half or two hours. That's why you want to know this, even if you never DIY!
At this time I am proceeding to seal the engine back up. Next, I'll reinstall the lower end stuff removed in earlier posts. pan baffles, oil sump pick up, oil pan. I'm fairly convinced there isn't much I can do with the innards of the Duratec, even crossing over to the generic side. At least for the moment.
On the other hand, there is plenty to do outside, with intake and exhaust. I have been very busy pursuing two options for more efficient exhaust. One is a moderate design using other Duratec parts and a cat back layout. The other involves a full blown header set with cat back also. I will be previewing both options in mock up very soon. There is still a lot of work to do with building crossover pipes, etc., but I'm feeling very optimistic about the exhaust. Both options, BTW, still fully utilize the factory ECM outputs and factory mapping. Then Karl Wolf has a muffler mod that I'll include in the final exhaust mod.
Hope you enjoy.